The Inert gas is produced in the IGG by the combustion of fuel with air. Marine diesel oil (MDO) or MGO is drawn from the storage tank and pumped through a filter to the main burners. A blower delivers the air necessary for combustion.
Oil and air is mixed in the correct proportion in an air-atomizing burner, which is ignited by the pilot burner. The fuel-air ratio and the oxygen content of the IG can be regulated by a valve in the fuel supply line to the main burner.
Purple-blue to rose-purple flame indicates good combustion whereas yellow flame means too much fuel oil or too low delivery air pressure causing low atomizing pressure and risk of soot formation.
The inert gas thus generated consists of mainly Nitrogen and carbon dioxide. It is first cooled in the combustion chamber by means of a sea water jacket, which surrounds the combustion chamber. The gas then comes in direct contact with a water spray. The resultant IG comprises of:
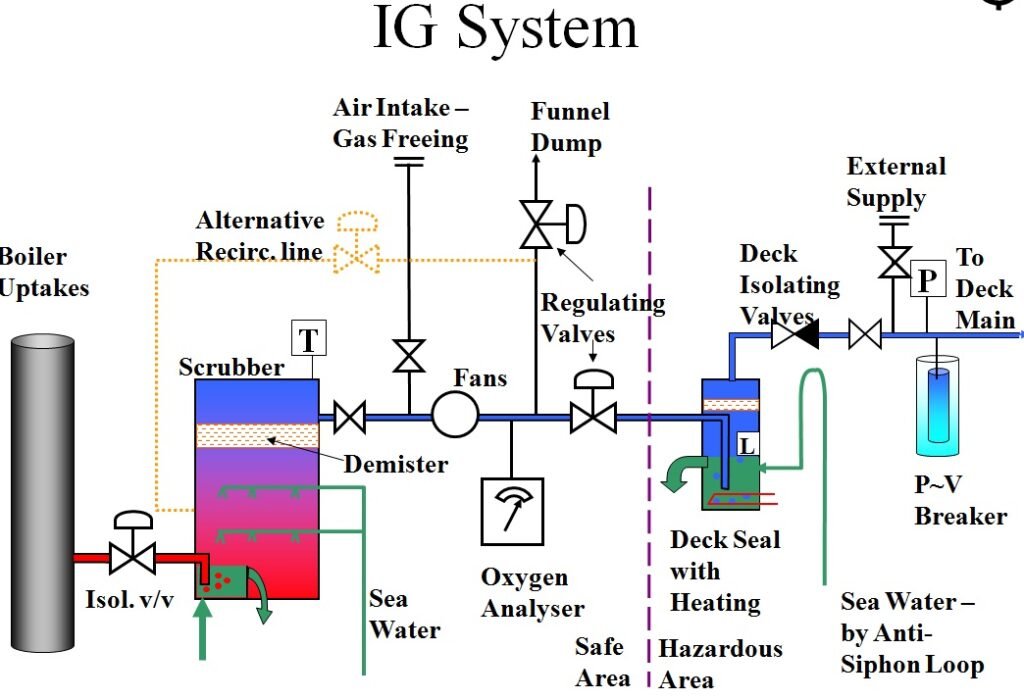
Oxygen : 2% by volume
Carbon dioxide: 13% by volume
Nitrogen : 85% by volume
Due to perfect combustion, there is a complete absence of soot. The temperature of the gas leaving the generator is about 5-10* above the cooling water temperature.
During the operation, should there be a reduction in demand for the IG, the excess gas is vented to the atmosphere. The operation is continuously monitored for flame, water or control air failure and excessive cooling water level. Should any emergency condition arise, the IGG automatically shuts off and sounds an audible alarm.
This is a costly installation, which is usually found in product or chemical tanker. With some clean cargo tainting could be a problem, if flue gas from boiler is used.
Chemical tankers & Product tankers are normally FRAMO tankers hence IGG is fitted on these ships, secondly the quality of IG plays a very important role in maintaining the quality of chemicals being transported.
Conventional tankers with turbine driven COP will always have a large water tube boiler and thus Inert gas on these ships will be produced from boiler flue gas. Boiler will be used continuously during cargo discharge for running the cargo oil pump turbines (COPT).
On Framo tankers, the cargo discharge system consists of each cargo tank having a fixed submersible cargo pump, this pump is coupled to a hydraulic motor. The hydraulic motor is driven by high pressure hydraulic oil (220 bar), this high pressure hydraulic oil is delivered by hydraulic power-packs located in the engine room, these power packs are normally driven by diesel engines.
Thus these ships use an IGG for production of inert gas. They do not have large boilers as no turbines are present, hence IG from boiler uptake is not possible.
Carbon Molecular Sieve type Nitrogen Generator
The molecular sieve nitrogen generating plant is usually installed on ships such as chemical carriers where oxygen critical cargoes may be carried and purity of the inert gas is of utmost importance.
The system uses the pressure swing absorption method using a carbon molecular sieve which has the unique property of absorbing oxygen in preference to and at a faster rate than nitrogen. When air passes through the molecular sieve, oxygen is absorbed.
Nitrogen gets across and is collected. However the sieve gets saturated with oxygen after sometime and needs to be changed over. The system uses two vessels packed with the carbon molecular sieve. The vessels are alternatively on line or in the process of regeneration. As one reaches saturation, the system switches to the second. Change over time is appox. 1 minute.
The oxygen from the saturated sieve is removed by applying a reduced pressure to the vessel and then venting to the atmosphere. The nitrogen gas thus generated is fed to a buffer vessel from where it is distributed to the inert gas line. The purity of the nitrogen depends on the flow rate and can be as high as 99.5%. The lower the flow rate, the higher the purity and vice versa.
You may also like, Why Knock Nevis was Scrapped – The death of Seawise Giant