Ethylene carriers are the most sophisticated of the semi-pressurized tankers and have the ability to carry not only most other liquefied gas cargoes but can also transport ethylene fully-refrigerated at its atmospheric pressure boiling point of -104°C. Designed to carry most liquefied gas cargoes except LNG.
Of this ethylene carrier fleet, about one dozen form a special sub-group of ships able to handle a wide range of liquid chemicals and liquefied gases simultaneously. The ships can load or discharge at virtually all pressurized and refrigerated terminals, making them the most versatile gas carriers in terms of cargo-handling ability.
Many ethylene carriers can also carry LPG cargoes, which increases their flexibility.They feature cylindrical or bi-lobe, insulated, stainless or low temperature nickel steel cargo tanks able to carry cargoes at minimum temperatures of -104ºC and at tank pressures of up to about 6 bar.
The ships can load and discharge at virtually all pressurised and refrigerated terminals, making them the most versatile LPG carriers in terms of cargo handling ability. Powerful reliquefaction units are installed.
Also Read Top 10 Biggest LNG Ship Carriers in the World – Latest 2023
Cargo Capacity
Cargo capacitiy depends on the trade for which the vessel was constructed and range from 1,500 – 15,000 cubic metres. Cargo capacity of Ethylene gas carriers is usually less than LNG/LPG carriers because of less demand in Huge quantities than LPG/LNG
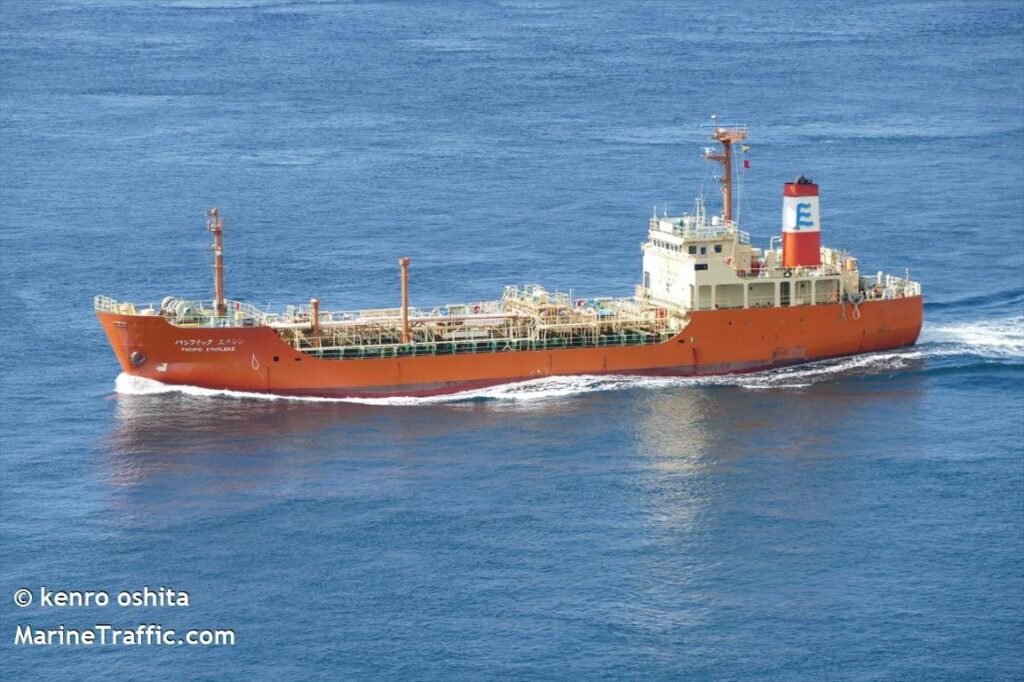
Temperature Control
Thermal insulation and a high capacity reliquefaction plant is fitted on this type of vessel.
Construction
Ethylene Carriers have Containment systems can either be Type C, Type B or Type A prismatic free-standing.
If Type C pressure vessel tanks are used, then no secondary barrier is required If Type B is used a partial secondary barrier is required If Type A is used a full secondary barrier is required. Because of the cargo temperature of -104°C, the hull cannot be used as a secondary barrier in this case and a separate secondary barrier must be fitted.
Ethylene ships have incorporated a grand variety of cargo tank shapes over the years, including spherical, prismatic and membrane tanks and longitudinally and transversely mounted cylindrical and bilobe tanks. Cargo tank materials compatible with the -104°C carriage temperature have included aluminium alloys and 5, 9 and 36 per cent nickel steels.
For reasons of economy, Type C tanks have predominated in this trade.
Ballast is carried in a full double bottom and wing tank ballast system.
Reliquefaction plant onboard Ethylene Carriers
Ethylene carriers are equipped with a cascade reliquefaction plant. The system consists of two
circuits: open and closed. The open circuit uses charge as a refrigerant that allows cooling of cargo
in cargo tanks, while the closed circuit uses propylene as a refrigerant
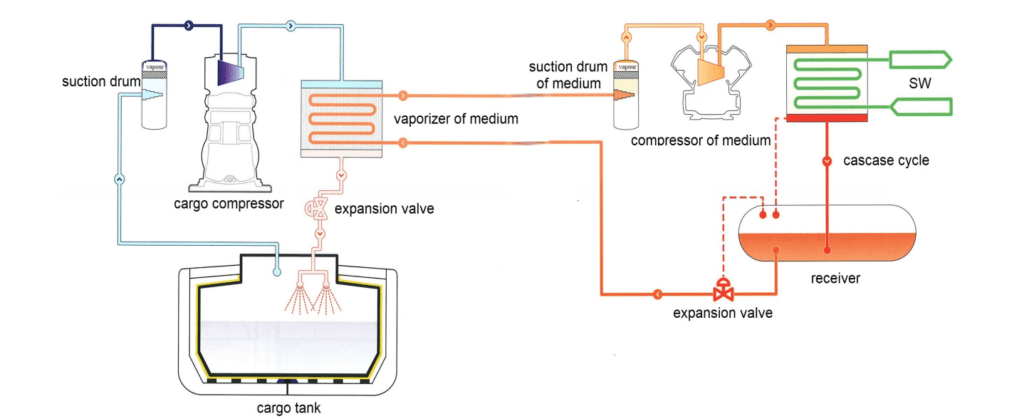
The Nitrogen content of condensed Ethylene vapour has a direct effect on the cooling capacity
of the cycle. The Nitrogen that creates with ethylene the mixture with a lower condensation temperature causes the stoppage the compressors due to the high condensing pressure. In order to avoid exceeding the operating pressure of the compressors, 18 bar during the cooling operation
of the cargo, the valves on the condenser are opened, hot Ethylene vapours are directed to the
cargo tanks and heat the load.
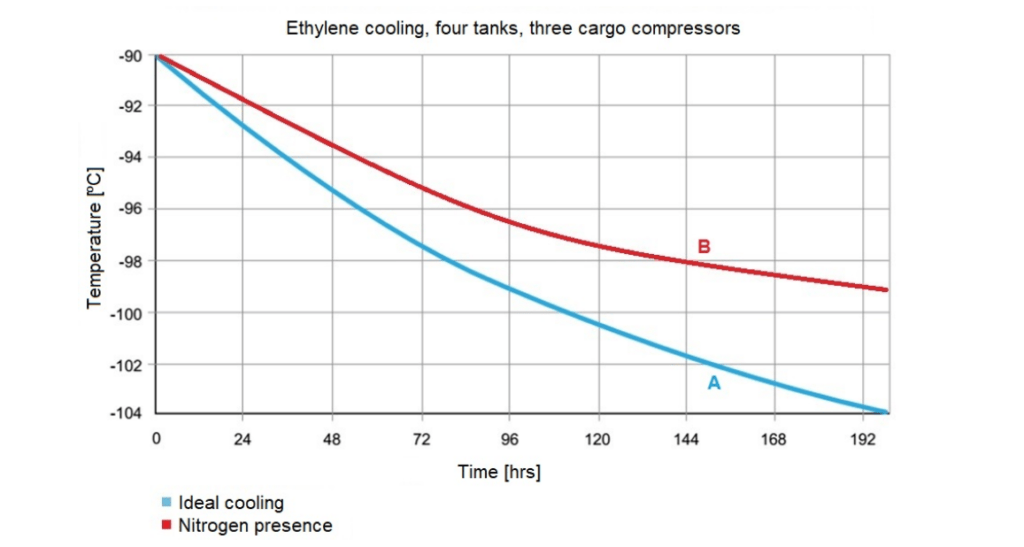
of the operation through a bottom line
The open valve significantly reduces the mass flow of condensate (Fig. 6), and thus the capacity cooling. With the lowering Ethylene temperature, the pressure in the tanks, and thus the suction of the compressor, decreases, which causes a decrease in cooling capacity of the cycle. This is shown by the curve A in Fig. 6. As the temperature of Ethylene decreases, the gradient of the time unit needed for its cooling increases.
This means that the more Ethylene need to be cooled, the more time the cooling process will take. Curve B shows the possible cooling speed with partial loss of a condensate mass flow with open valve on the condenser.
Use of Portable Gas Detectors onboard Ethylene Carriers
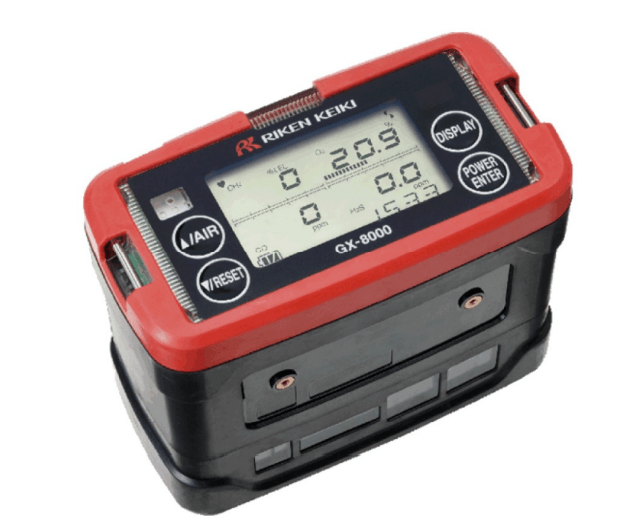
The gassing-up operation is completed when in tank the concentration of Ethylene vapour should be 100%. To measure this concentration a portable gas detector Riken Keiki GX-8000 is used.
The detector (Fig. 7) is a gasometer device with built-in electrochemical sensors or a galvanic cell containing electrolytes. It allows analysing the concentration of gases such as: Oxygen, flammable gases, toxic gases (Carbon monoxide and Hydrogen sulphide) in the air and high concentration of flammable gases in Nitrogen and inert gases. The measurement margin of error of this device is 5%.
A common problem on ships when measuring hydrocarbon concentrations during gassing-up operation of cargo tanks is not enough accuracy of the device. In order to properly carry out this process, measurements of inert gas concentration in such a mixture like Nitrogen and Ethylene must have a minimum accuracy of 1.5%.
The GX-8000 gas detector does not provide this option. In addition, this model in the GX-8000 version is not suitable for analyses of high hydrocarbon concentrations.
Factors affecting the proper carrying the gassing-up operation, as well as minimizing cargo loss, are many. A thorough analysis of the method of carrying out this operation using Ethylene vapour should be made, as well as the lack of use during gassing-up the vaporizer, which is inconsistent with the instructions on the ships.
Gassing-up in a cascade is not an optimal method, on contrary; it generates substantial loss of Ethylene, which translates into financial losses.
In addition, it is necessary to look at the device used to measure the concentration of hydrocarbons in cargo tanks, which is very inaccurate to measure high hydrocarbon concentrations. Inappropriate measurements make difficulties during the most demanding cargo handling operation, which is a gassing-up process.
Must Read 10 Nakilat Shipping Facts – Qatar Gas LNG Shipping
History of Ethylene Carriers
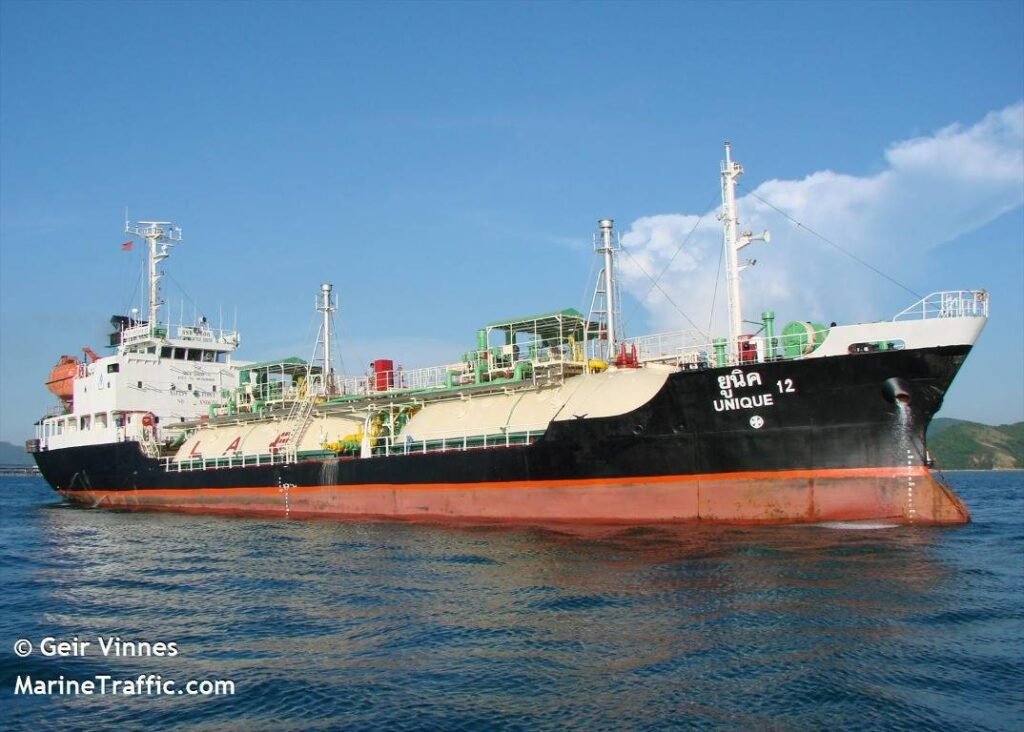
Ethylene has an atmospheric boiling point of -104°C, about halfway between that of LPG at -48°C and LNG at -163°C. Liquefied ethylene gas carriers (LEGCs) have been constructed as either fully refrigerated ships with the cargo at atmospheric pressure or semi-pressurised/fully refrigerated (semi-ref) ships with pressure vessel cargo tanks.
A total of 135 ships able to transport ethylene have been built or converted since the early 1960s and, of these, 28 are no longer trading. Of the 135 ships, 10 vessels ranging in size between 630m3 and 29,400m3 were designed with the ability to carry LNG, ethylene and LPG cargoes.
The initial ethylene trade routes were established around the coasts of Europe, Mexico and Japan. In addition to all those cargoes carried by a semi-ref LPG carrier, a typical LEGC could also trade with ethane, ethene and ethylene, ensuring the longest cargo list of all the gas carriers.
10 Facts about Ethylene Carriers
- The first ethylene carrier built in Japan was the appropriately named Ethylene Maru No 1 which was delivered from Ishikawajima Ship and Chemical Company in Tokyo in 1965. The ship had a single, horizontally mounted, cylindrical cargo tank with a minimum design temperature of -30°C and a maximum design pressure of 7 barg.
- However, because even the largest LEGCs have relatively limited overall ship dimensions, many small and medium-size shipyards are able to compete for orders for such ships. The accompanying table of LEGC deliveries by country of build, featuring the first such ship from each yard and the first vessel in any notable series, indicates the progress in ship size over the evolution of these sophisticated gas carriers with cargo lists that are second to none. LPG
Source: History about Ethylene Gas Carriers
- To begin with, it is worth emphasizing that the content of Oxygen in Nitrogen in cargo tanks must be reduced to minimum, depending on the next cargo, not exceeds even 0.1%. Tab. 1 presents permissible Oxygen concentration in the tank for exemplary loads together with operations that must be done between loading different cargo.
- Properly working pressure swing adsorption (PSA) system, which generates Nitrogen used to tank inerting, is very important for further operations.
You may also like,
- Top 10 Biggest LPG Ships of 2023
- Top 10 Biggest LNG Ship Carriers in the World – Latest 2023
- Esso Northumbria – 10 Facts about the Largest Ship of 1971
- Why Knock Nevis was Scrapped – The death of Seawise Giant